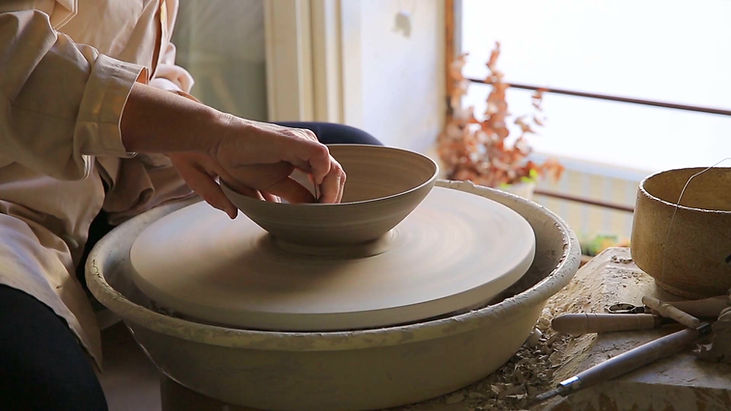
OUR Showcase
At ECIC Consulting, we take pride in our work and strive for excellence. Our showcase below highlights some of the projects we have successfully completed. Explore our work and see how we can help your business succeed.
Project Portfolio
​​
-
Complete design and build out of 30,000 square foot Sausage Manufacturer space in Carlstadt, New Jersey. Production Capacity increase on 4X with new space and process flow. Facility Was built out to accommodate for USDA guidelines and other food safety guidelines.
-
Expansion design for a 20,000 square foot premium ice cream manufacturer in Brooklyn New York. Designed a water and energy saving system to cut water consumption by 75% with an integrated Mokon closed loop double wall cooling system package mounted to the building roof. Laid out plans to double packaging capacity in the existing space with faster 4 up filling equipment and a second pasteurization processing tank to continuously feed the farm tanks that keeps the filling system running throughout the entire production shift.
​
-
ERP Implementation support for a 100 Million dollar conveyor manufacturer in St Matthews Kentucky. Redesigned Robotic cell work flow to increase throughput from 12 units per day to 22 units per day with the same staffing.
-
Site assessment for acquisition by major retailer and Facility redesign design for 60,000 square foot, $21m Closet Manufacturer acquisition. Facility dust collection corrections for OSHA and NFPA compliance with workflow and quality improvements for 99% defect reduction in 2 weeks. New equipment acquisition and preparation for second location expansion in Southeast USA region.
​
-
Increased overall Glass fabrication production performance for New Jersey Glass Fabrication company with implementation of Process KPI metrics. Implemented quick expansion into PVB Glass lamination. Sourced and installed PVB double Vacuum furnace to insource 1.3 million in purchased PVB laminations within 2 months of start. Redesigned Seam wash to temper line to implement Tech Glass digital printer along with Custom built clean room for the digital printer. Floor plan changes also reduced material handling for all cut seam and wash processes while utilizing the existing Glass washing equipment. Process changes and morale improvements cut lead times from 8 weeks to 4 weeks.
-
National Roll out of Custom Closet Manufacturing for major US Retailer. Selected acquisition in Chicago and Florida. Performed full assessment of Chicago production facility with recommendations for corrections to improve facility output. Corrected Chicago non-compliant Dust collection system to prevent OSHA and Fire code shut down. Re designed production floor plan along with outdoor dust collection system to increase sales capacity from 24M to 60M annually in the same footprint. Florida expansion to follow as well as a third as sales growth continues.
-
78,000 Sf Expansion Food facility build out and project management in Cincinnati Ohio. Refrigeration Design, floor plans and automation selection and implementation. Multi-phase launch plan from startup through full scale production for 150 person facility. $480,000 in State and local incentives facilitation for the facility startup.
-
Facility selection and space utilization planning for new Jersey based Sausage manufacturing company. Assessed several facilities for suitability and potential floor space utilization as well as electrical plumbing and cooling requirements.
​
-
Relocation of a 60-million-dollar automotive lighting and accessories manufacturer from Newark, New Jersey to Orlando Florida. Equipment logging work instructions development for new hire training and operations.
-
Relocation of an 80M aerospace navigation device manufacturer, Consolidation, and relocation from a 375,000 square foot facility in Little Falls New Jersey to an 80,000 square foot facility in Pine Brook New Jersey. Designed manufacturing floor plan, clean room, DI Water loop, Electrical planning, and design. Rationalized and eliminated large amounts of equipment for new smaller capacity and footprint. Designed and integrated process cooling systems for energy savings for coating processes
-
Relocation of an architectural glass fabrication business from a 40,000 square foot facility in Passaic, New Jersey to a 90,000 square facility in Wayne New Jersey. Complete facility layout. Project management of build out budgeting. Facility shut down planning relocation logistics and plant startup. Ongoing Business process improvements.
​
-
Relocation of a 40M Medical equipment manufacturer from Springfield New Jersey to a 45,000 square foot facility in Pine Brook New Jersey. Designed manufacturing floor plan, plumbing, compressed air and warehouse for relocation.
​
-
Construction of an 800 square foot 3D Metal printing laboratory in Clifton New Jersey. Full design of showroom, HVAC, Electrical Venting, Permitting and construction management. Marketing showroom for state-of-the-art 3D metal X printing product. https://markforged.com/
-
75,000 square foot expansion of an industrial roll forming and fin tube manufacturing company. Redesigned production flow to reduce motion and improve delivery time as well as strategically positioned materials warehousing in Wayne New Jersey. Floor plan layout for LEAN flow, Full Electrical Design and permitting.
​
-
Relocation of a 65,000 square foot facility in Franklin New Jersey for an industrial baking oven manufacturer with implementation of cellular manufacturing process. Complete floor plan and warehouse layout for welding, metal fabrication and assembly.
-
Complete Relocation, staffing and project management of a custom Lighting manufacturer from Brooklyn, NY to a completely renovated 32,000 square foot facility in Trenton, NJ. Full project management and reviews with city planning board. Manufacturing process included implementation of cellular manufacturing concepts. Fully staffed the company with all new employees and trained staff on assembly process.
​
-
Relocation and consolidation of a 12M division of an automotive accessories manufacturer from Laurinburg, North Carolina to Newark New Jersey, resulting in a 40% reduction in space over the previous location. Full Project management and logistics of relocation . Facility design, Ventilation, electrical and floor plan. Developed over 40 procedures for standard work for training.
​
-
Relocation and complete redesign of a cosmetics manufacturing facility in Patterson New Jersey to a 32,000 square foot facility in Orangeburg New York. Full Facility and warehouse floorplan, Electrical plumbing and compressed air systems.
​
-
Redesign Expansion of a 37,000 square foot custom closets manufacturer in Maryland with implementation of cellular manufacturing. Revised workflow and improved output to support sales growth over 30%. New panel saw, nested base router and pod and rail routers with drawer box assembly work center. Full Floor plan and dust collection systems with warehouse and sub assembly work cells.
​
-
Expansion of 30,000 square foot expansion to a 50,000 square foot facility for a machinery manufacturer in Poughkeepsie New York with implementation of cellular manufacturing concepts. Full floorplan, demolition plans and revisions for town zoning variances.
​
-
Relocation of an Industrial Boiler and hot water heater manufacturing facility from Northvale New Jersey to Orangeburg New York. Relocated a 40,000 square facility into a green fields 90,000 square foot facility.
-
Onshoring a high purity semiconductor valve product line form Nobeoka, Japan to Malden, Massachusetts. Full Clean room and DI water system design. Training and documentation. Setup of CMM and plastics dedicated CNC equipment and ultrasonic part washing.
​
-
Relocation of double wall pipe fabrication facility form Montgomery Alabama to Malden, Massachusetts.